Porosity in Welding: Identifying Common Issues and Implementing Finest Practices for Avoidance
Porosity in welding is a prevalent concern that often goes unnoticed until it causes substantial issues with the integrity of welds. In this conversation, we will explore the crucial elements contributing to porosity development, analyze its destructive impacts on weld performance, and review the ideal practices that can be taken on to decrease porosity event in welding procedures.
Typical Causes of Porosity
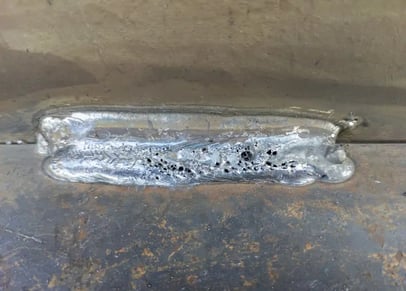
Using filthy or wet filler products can introduce contaminations into the weld, adding to porosity problems. To mitigate these common causes of porosity, extensive cleaning of base steels, correct shielding gas selection, and adherence to optimal welding parameters are important practices in achieving premium, porosity-free welds.
Effect of Porosity on Weld Top Quality

The presence of porosity in welding can considerably jeopardize the structural stability and mechanical buildings of welded joints. Porosity produces spaces within the weld steel, compromising its total stamina and load-bearing capacity.
Welds with high porosity degrees often tend to exhibit lower effect strength and lowered ability to warp plastically before fracturing. Porosity can restrain the weld's capability to properly transfer pressures, leading to premature weld failing and possible safety dangers in important structures.
Finest Practices for Porosity Prevention
To improve the architectural stability and quality of welded joints, what particular procedures can be implemented to minimize the occurrence of porosity throughout the welding process? Utilizing the proper welding technique for the particular material being welded, such as adjusting the welding angle and gun placement, can even more stop porosity. Normal evaluation of welds and immediate remediation of any try this website kind of concerns determined during the welding process are vital techniques to protect against porosity and create high-grade welds.
Significance of Correct Welding Strategies
Applying correct welding techniques is vital in ensuring the structural stability and high quality of bonded joints, building upon the foundation of effective porosity avoidance procedures. Too much warm can lead to increased porosity due to the entrapment of gases in the weld swimming pool. In addition, making use of the ideal welding specifications, such as voltage, existing, and travel speed, is essential for accomplishing sound welds with marginal porosity.
In addition, the choice of welding procedure, whether it be MIG, webpage TIG, or stick welding, need to straighten with the specific needs of the task to make certain optimal results. Correct cleansing and preparation check this site out of the base metal, in addition to selecting the appropriate filler product, are also important parts of competent welding methods. By sticking to these ideal techniques, welders can minimize the threat of porosity formation and generate top notch, structurally audio welds.

Testing and Quality Control Actions
Quality control actions play a crucial function in verifying the honesty and reliability of bonded joints. Evaluating treatments are vital to detect and prevent porosity in welding, making sure the strength and durability of the end product. Non-destructive screening methods such as ultrasonic screening, radiographic screening, and visual assessment are commonly employed to identify possible defects like porosity. These methods enable the evaluation of weld top quality without compromising the stability of the joint. What is Porosity.
Post-weld assessments, on the other hand, assess the last weld for any problems, consisting of porosity, and verify that it meets defined criteria. Executing an extensive high quality control strategy that consists of complete screening treatments and evaluations is critical to decreasing porosity concerns and making certain the overall high quality of welded joints.
Verdict
Finally, porosity in welding can be a typical problem that influences the high quality of welds. By determining the common reasons for porosity and applying finest practices for avoidance, such as appropriate welding techniques and testing measures, welders can make sure high quality and reliable welds. It is important to prioritize prevention approaches to minimize the incident of porosity and preserve the honesty of welded structures.